編集: 2018/02/27
校正、追記など: 2020/10/15
Mach3 はCNCに興味がある人は誰でもご存知と思いますが、自作や市販機改造など多くのホビーユーザ(生産現場でも?)が使っているコントローラです。
音速の単位で知られているのでドイツ語読みのマッハと発音する人が多いですが、英語ではマーク[mɑːk]あるいはマク[mæk]です。
今はMach4が出ていますが、まだまだMach3は国内でもユーザーが多いのでネット検索で山のように情報が得られます。日本語バージョンはありませんが、ユーザーフォーラムは大規模なものでとても参考になります。
ライセンスを購入する前はトライアル版(Gコードが確か500行しか実行できない)として使えますが、ライセンス購入後は10,000,000行まで実行可能です。
また、操作画面の見かけを変えるのに有償無償合わせてたくさんのScreensetがあり、ソフトの知識があれば自分で画面を編集できるようにもなっています。
私は、ツールパス表示部分が大きいのと見た目がシンプルなのが気に入って、標準の1024.setではなく、最初から下のような 2010 Screensetを使っています。
ユーザーが増えてほしいと願っているんですが、国内には誰もおられないようです。
2020/10/15 追記:
ベンダーに聞いてみたら、日本で10人余りがライセンスを買っておられるようです。
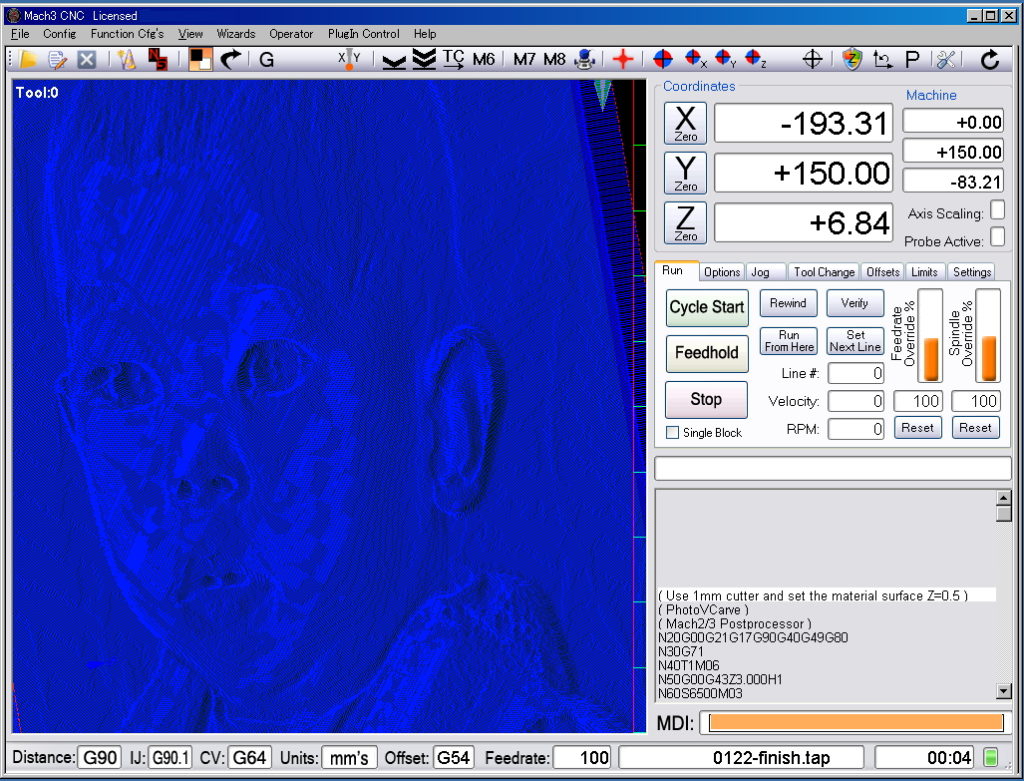
上のツールパス画面は写真(jpg)をPhotoVCarveで生成したものですが、Gコードは約100,000行、加工に数時間かかります。
2010 Screenset のユーザーを増やすため(?)、主な操作・設定の説明をしておきます。
上の写真は運転画面(Run)ですが、他の設定は画面右側中央のRun〜Settingsのタブで切り替えます。
Run 運転
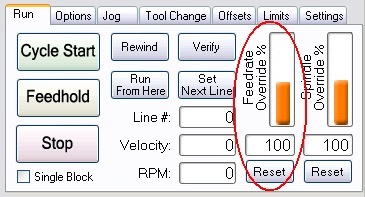
Cycle Start = 加工開始
Feedhold = 一時停止
読込み中の行を完了して停止
スピンドルは止まりません
Cycle Start で運転再開
Stop = 停止、スピンドルも停止
Feedrate Override % は、マウスで上下にドラッグすると速度調整ができますが、数字を打ち込んでも変えられます (最大値は250%)
Jog ジョグ (手送り)
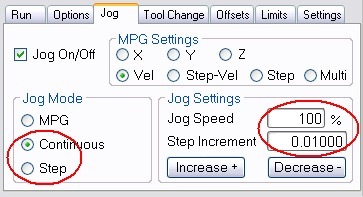
Jog Mode = 動作の切り替え
MPG (ペンダントなど)
Continuous (連続)
Step (設定量だけ)
Jog Setting = 現在の設定量
Jog Speed (連続送り速度)
Step Increment (設定量)
いずれもキーボードの➕、➖ ボタンで増減、設定値は Settings タブで指定
キーボードからの各軸送りボタンは(Mach3基本設定のままであれば);
X+ : ⇨ X-: ⇦ Y+: ⇧ Y-: ⇩ Z+: PgUp Z-: PgDn
Tool Change 工具交換の設定
エンドミルなどを交換した時のZ軸ゼロを設定
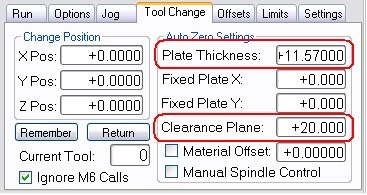
Auto Zero Settings
Plate Thickness = プレートの厚さ
Clearance Plane = ゼロ点を検出して戻る位置
写真のようにセットして、メニューバーの
をクリックするとスピンドルが下がって±0.01 程度の精度でゼロ点を検出します。
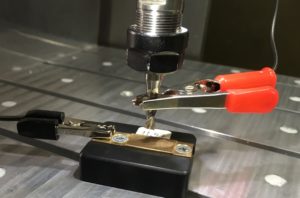
クリックする前に必ず、プレートと工具をタッチさせて 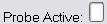
のランプが緑になるのを確認します。
タッチした時に導通が無いと、工具を破損する可能性があります。
プレートは、写真のようにアクリルなど絶縁体の上に金属板を載せたようなもので、タッチしたときに変形しないように作ります。
プレート底面(=加工物の上面) が Z 0 になり、Clearance Plane (上の例ならZ 20) まで上がって停止します。
Tool Change と Probing を使うには、Mach3 の設定と、信号を入れるための電線+クリップが必要です。
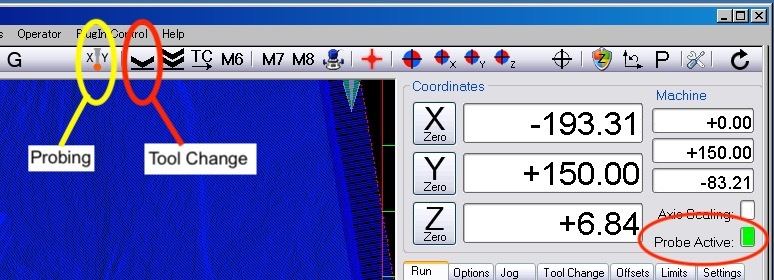
Mach3 – Config – Ports & Pins – Input Signals – Probe の設定
パラレルポートの入力に使えるピンを設定 (13ピンを設定)
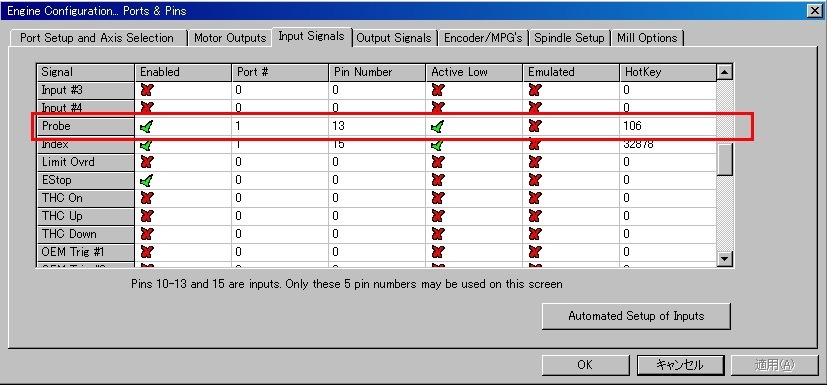
HobbyCNC ボードの入力は10kΩでプルアップされているので、13ピンとグランドへ配線するだけで使えますが、プレートが13ピン側になるので機械の金属部と接触しないよう絶縁する必要があります。
上の写真ではエンドミルをつかんでいるクリップがグランド側になります。
(クリップを付け間違ったので赤色になっていますが、直すのが面倒なので …)
エンドミル側はグランドにつながっていますが、不安定なので、必ず基板のグランドから引っ張ってこないと危険です。
ワークにプレートを載せ、アイコン
をクリックすると;
下降 250mm/min > 通電確認 > 2mm上昇 > 下降 25mm/min > 通電確認 >上昇
という動作で、工具先端がワーク上面(ゼロ点)からClearance Plane の値まで上昇します。
マクロ(M889.mls)を編集すれば速度などは変えられます。
Settings ジョグ速度の設定
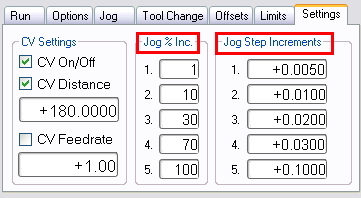
Jog % Inc. = 早送り速度(G0)に対する%
Jog Step Increments =Step送りの単位で、各軸のボタンを押すごとに進む量
それぞれ5段階の設定で、+、− ボタンを押すごとにサイクリックに変わります。
Options
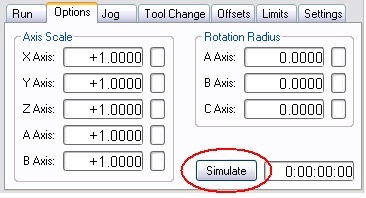
Optionsタブの Simulateで、ピッタリではないですが、加工時間の予想ができます。
Probing
これらの他に、Probingという画面があり、ワークのXY平面上の位置を読み込んで原点出しに使うことができます。円柱状のワークの中心、丸穴の中心、ポケット加工の中心なども読み込めます。
便利に使えるので、詳しく説明しておきます。
メニューバーの Probing アイコン
をクリックすると、下の画面が現れます。
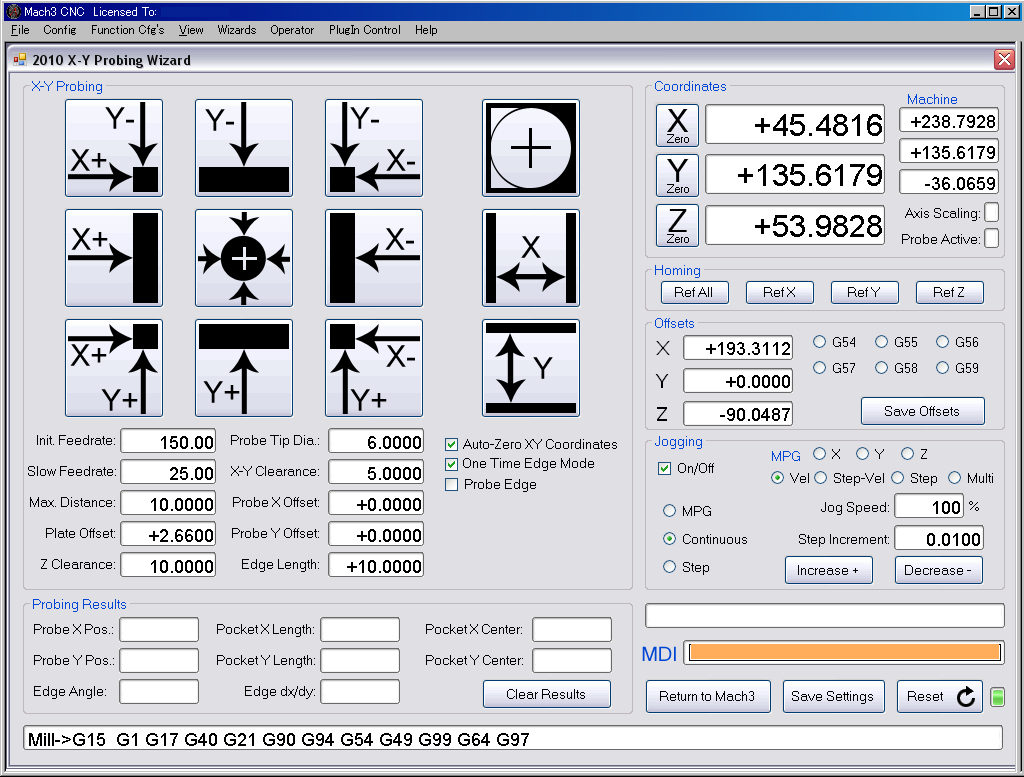
例えば、スピンドルにプローブとして6mmのロッド(エンドミルのシャンクなど)をセットしてグランド側のクリップでくわえておき、ワーク側を13pin側のクリップでくわえます。
ワークが本体と絶縁されていれば(=両面テープで固定されているなど)、13pin側のクリップをワークに当てておけば問題ないですが、金属製のクランプなどで固定されている場合はちょっとしたアダプタみたいなものが必要です。
ワークがアクリルなど絶縁体の場合も同様です。
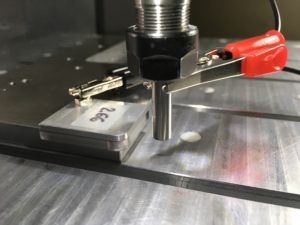
下の写真は、左がエッジ用、右がコーナー用です。コーナー用はエッジ検出にも使えますが、ワークによって使えない場合があるので、エッジ用を別に作りました。
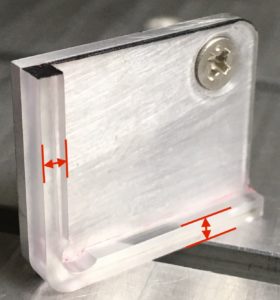
いずれもアルミ板にアクリル板を接着して削ったものです。コーナー用のアダプタは、L型の両方が同じ寸法になるように加工しておかなければなりません。
いずれも、Tool Change のプレートを兼ねることもできます。
上の写真に描き込んである部分(赤色矢印)の実寸法を

に入れておきます。アダプタを変えたときには、忘れず変更してください。
コーナーの測定は、すべて時計回りに動きます。
>
= X軸が+に動き、その後Y軸がー
>
= Y軸がーに動き、その後X軸がー
>
= Y軸が+に動き、その後X軸が+
>
= X軸がーに動き、その後Y軸が+
> 円柱の場合は Y+からスタート、Z方向にかわしながら、Yー、X+、Xー の順
注意点:
コーナー検出の場合は、プローブをコーナーから約38mm以内に位置させてスタートします。元の値が1.5 inch(38mm)ですが、それぞれのマクロを編集すれば変えられます。下の図は、
の動作です。
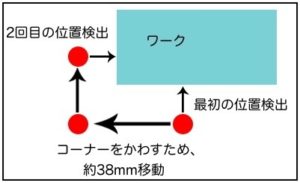
その他の入力は次の通り;
:プローブの接近速度
:再接近速度
:検出までの最大距離 (大きすぎても問題なし)
:アダプタを使用する場合のオフセット (上の説明参照)
:円柱測定の場合、移動時にZ軸を引き上げる距離
:スピンドル側につけたプローブ(ロッド) 外径
:測定後の退避距離

:プローブがスピンドル中心でない場合の距離 X、Y
:エッジ検出の際に、指定した距離で2回測定
(下の
参照)
数字がマイナスの場合は、2回目はその軸のマイナス方向へ動く
円柱測定の場合は、直径以上の値を入力 円柱の芯出しは=>
:測定後にエッジあるいはコーナーの座標をゼロにセット
Probe Edge の場合はゼロにならず、Probing Results に座標が表示されます。
:誤ってプロービング動作に入らないようチェック
:チェックを入れると、エッジの2ヶ所を測定し、その軸に対する角度と2点の差を測定 (測定完了すると、チェックは外れます)
測定結果は、次のように表示されます; 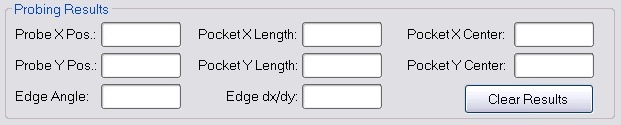
Probe X Pos 、Probe Y Pos = 最初に検出したエッジの座標
Edge Angle = 2点の差 (Edge dx/dy) と距離 (Edge Length) から計算した角度
Pocket X Length 、Pocket Y Length = ポケット測定の場合の各方向の幅
Edge dx/dy = 2点の差
Pocket X Center 、Pocket Y Center = ポケット測定の場合の各方向の幅の中心座標
ハンドコントローラ
ワークの位置決めなどをするのに、Config > System Hotkeys を使って矢印キーなどを設定しますが、フルキーボードは大きすぎて取り回しが悪いので、USB接続のテンキーパッドを使っています。
2010 Screensetでは、RunやJogなど画面切り替えするのにMach3のHotkeysでは割り当てできず、テンキーをカスタマイズできる「DressKey:簡単にテンキーをカスタマイズしよう」を使って簡易コントローラを作りました。
<2021年2月20日追記:上のDressKeyのサイトは昨年閉鎖されたようです>
このソフトは、AutoHotKeyというスクリプト言語を使って入力を簡単にし、日本語化したものです(と書いてありました)。
ただ、理解が足りないのか一部の設定がうまくいかず、結局AutoHotKeyのスクリプトを作りました。
AutoHotKey はネット検索するとたくさんの使用例や解説があります。
無線接続のテンキーパッドもありますが、うまく設定できないという情報もあり、とりあえずはケーブル付きです。
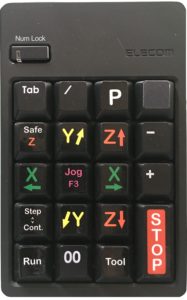
Run = 運転画面に切り替え (Cycle Startではありません)
Jog F3 = ジョグ画面へ
Step<>Cont = ジョグ時のステップと連続の切り替え
Tool = Tool Change 画面へ
Safe Z = Z軸の退避 (Machine Coordinate のゼロへ戻る)
P = 全軸の退避(Z – Y – X の順に原点へ戻る)
STOP = EStop
これら以外の、各軸の+、ーなどはMach3のHotKeysの設定です。使うときは、適当なジッパー付きポリ袋に入れてゴミ除けにしています。
/////